- Agricultural Economics
- Animal and Food Sciences
- Biosystems and Agricultural Engineering
- Community and Leadership Development
- Entomology
- Extension and Education
- Extension Administration
- Forestry
- Horticulture
- Human Environmental Sciences
- Landscape Architecture
- Livestock Disease Diagnostic Center
- Plant Pathology
- Plant and Soil Sciences
- Veterinary Science
Search research reports:
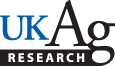
Precision Placement of Crop Production Inputs via Distributed Control
S. Shearer, T.S. Stombaugh, C.R. Dillon
Department of Biosystems and Agricultural Engineering
Project Description
Recent trends in agricultural field machinery exploit the use of microcontrollers to enhance machine function. Controller Area Networks (CAN) were developed to facilitate communications between microcontrollers. Off-target placement of crop production inputs is a costly and time consuming problem for agricultural producers. Typical seeding/application problems include: skipped areas, double treatment, unintentional treatment, or treatment of environmentally sensitive areas. Reducing or eliminating off-target treatments is increasingly important in a society that places high value on environmental quality and to global markets that are extremely competitive.
The goal of the proposed research is to develop a CAN-based distributed control systems for precision placement of crop production inputs such as seed, fertilizer, and pesticides. This control system will utilize dedicated microcontrollers for single element metering of inputs. Dynamic adjustment of machine operating parameters such as seed meter air pressure and shaft speed will be made in response to feedback from rate sensors, ground speed radar, and GPS position fixes.
Precision placement of inputs will improve Kentucky farm profitability through increased crop yield and minimized input costs through the elimination of skipped and doubled treated regions within a field, and by maintaining desired fixed and variable seeding/application rates across the toolbar or effective application width while turning and in point row regions of a field.
The proposed control system represents a significant advance and is warranted in view of increasing input costs and the need for traceability. Single nozzle control was achieved through the implementation of a Zynx X15 Controller with 30-Channel Spray ECU on an AgChem, RoGator 664 self-propelled sprayer (24 m boom) on a grain farm in Shelby County, Kentucky.Although not a CAN-based control system, the results of this investigation parallel thoes expected from CAN control.
Results are summarized for three fields highlighting the potential of this technology when applied to U.S. grain enterprises. A 15% minimum reduction in the total quantity of glyphosate applied was achieved using the single nozzle control approach. Returns on investment, achieved through reduced herbicide savings, will easily justify the capitol expenditures necessary to implement this technology for intermediate to large U.S. grain enterprises. Ancillary benefits accruing to the implementation of this technology will include preservation of environmentally sensitive areas of fields such as vegetated waterways and filter strips. Current spray application technology limits the producer's ability to control applications of herbicides, such as glyphosate, to a resolution of approximately 10 m or greater with large self-propelled sprayers.
Impact
The return on this investment from the implementation of CAN-based controls systems on agricultural field machinery will be a reduction in applied quantities of pesticides and nutrients that accrues to users by not double treating areas of the field where boom overlap is unavoidable. Producers with self-propelled sprayers managing multiple farms and fields will easily pay for the adoption of CAN enabled, map-based spray nozzle control in as little as a single cropping season.